
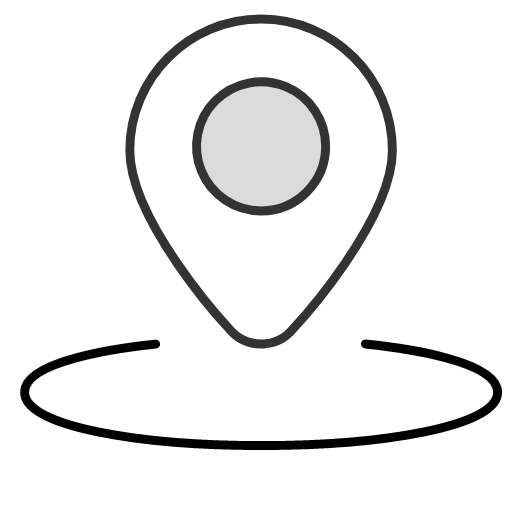
2.2), three-stage pumps can attain about 2 mbar and four-stage diaphragm pumps can reach about 5♱0^(-1) mbar.ĭiaphragm pumps offering such a low ultimate pressure are suited as backing pumps for turbomolecular pumps with fully integrated Scroll stages (compound or wide range turbomolecular pumps). LEYBOLD can attain about 10 mbar (see Fig. In the case of single-stage diaphragm vacuum pumps the attainable ultimate pressure amounts to approximately 80 mbar. Diaphragm vacuum pumps are not capable of attaining a higher compression ratio than the ratio between “dead space” and maximum volume of the pumping chamber. Thus volumetric efficiency worsens continuously for this reason. The quantity of gas which remains at the exhaust pressure expands into the expanding pumping chamber during the subsequent suction stroke thereby filling it, so that as the intake pressure reduces the quantity of inflowing new gas reduces more and more. In the case of this pumping principle a volume remains at the upper dead center – the so called “dead space” – from where the gases can not be moved to the exhaust line.
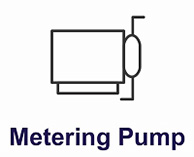
It is thus well suited for vacuum applications in the chemistry lab.ĭue to the limited elastic deformability of the diaphragm only a comparatively low pumping speed is obtained. Inlet and exhaust valves of a highly fluorinated elastomer as in the case of the DIVAC from LEYBOLD, it is then possible to pump aggressive vapors and gases. When coating the diaphragm with PTFE (Teflon) and when manufacturing the Diaphragm and valves are the only components in contact with the medium which is to be pumped.
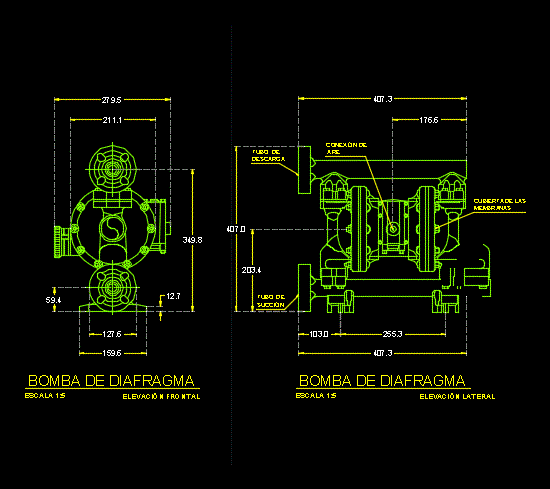
The diaphragm provides a hermetic seal between the gear chamberĪnd the pumping chamber so that it remains free of oil and lubricants (dry compressing vacuum pump). During compression, the pumping chamber is linked to the exhaust line. The valves are arranged in such a way that during the phase where the volume of the pumping chamber increases it is open to the intake line. The pumping or compression chamber, the volume of which increases and decreases periodically, effects the pumping action. It is moved in an oscillating way by means of a connecting rod and an eccentric. Of a diaphragm is tensioned between a pump head and the casing wall (Fig. Diaphragm vacuum pumps are single or multi-stage dry compressing vacuum pumps (diaphragm pumps having up to four stages are being manufactured). By design, no oil immersed shaft seals are required. Compared to rotary vane pumps, the pumping chamber of diaphragm pumps are entirely free of oil. Overall, a diaphragm vacuum pump can save up to 90 % of the operating costs compared to a water jet pump. They are alternatives to water jet vacuum pumps, since diaphragm pumps do not produce any waste water. Recently, diaphragm pumps have becoming ever more important, mainly for environmental reasons.
